Running a successful supermarket isn't just about stocking shelves; it’s about ensuring that your shelves are always stocked with the right products at the right time. A well-optimized supermarket reordering process is the backbone of efficient inventory management. Yet, many supermarket managers face challenges like overstocking, understocking, or delays in replenishment.
Here’s how you can streamline your supermarket reordering process and keep your customers satisfied while reducing unnecessary costs.
1. Understand Your Sales Patterns
The first step to an effective supermarket reordering process is knowing what your customers buy and when. Analyze your sales data to identify trends:
Which products sell faster during weekends or holidays?
Are there seasonal trends that affect certain items?
Which products experience consistent demand?
Using this data, you can forecast demand more accurately and prioritize reordering.
2. Categorize Your Inventory
Not all products require the same level of attention. Use the ABC analysis method:
A Items: High-value, low-volume products (e.g., premium cheeses).
B Items: Moderate-value, moderate-volume products (e.g., branded snacks).
C Items: Low-value, high-volume products (e.g., bottled water).
Focusing more frequent reordering efforts on A and B items will help streamline your supermarket reordering process, ensuring optimal stock levels.
3. Automate Wherever Possible
If you’re still relying on manual tracking, it’s time to embrace automation. Modern supermarket management software can monitor stock levels, send alerts for low inventory, and even place orders automatically. Automation saves time, reduces human error, and enhances the efficiency of your supermarket reordering process.
4. Set Clear Reordering Thresholds
Define reorder points for each product based on:
Average daily sales
Lead time from suppliers
Safety stock to cover unexpected demand
For example, if you sell 10 units of a product daily and it takes 5 days for delivery, you should reorder when stock reaches 70 units (10 x 5 + a safety stock buffer). Establishing these thresholds is a key step in optimizing your supermarket reordering process.
5. Build Strong Relationships with Suppliers
Reliable suppliers are critical to an efficient supermarket reordering process. Maintain open communication and negotiate flexible terms. Ensure that suppliers can handle sudden spikes in demand and deliver promptly. Building trust with your suppliers often results in better deals and priority during busy periods.
6. Regularly Review Inventory Performance
Reordering isn’t a one-and-done task. Schedule regular reviews to assess:
How well your reorder thresholds are working
Whether any products are frequently overstocked or understocked
Opportunities to renegotiate supplier terms
Adjust your supermarket reordering process based on real-time performance and customer feedback.
7. Train Your Team
Your staff plays a key role in the supermarket reordering process. Train them to identify inventory issues, use reordering tools effectively, and maintain accurate records. A well-informed team ensures smooth day-to-day operations and prevents costly mistakes.
8. Monitor and Reduce Wastage
Overordering leads to spoilage, especially for perishable goods. Track product expiry dates and optimize reorder quantities to minimize waste. Don’t forget to explore donation options for items nearing expiration instead of letting them go to waste. Managing waste effectively is an integral part of a successful supermarket reordering process.
Conclusion
Optimizing your supermarket reordering process isn’t just about saving money—it’s about ensuring a seamless shopping experience for your customers. With the right tools, data, and practices in place, you can strike the perfect balance between availability and cost-efficiency.
Need help fine-tuning your supermarket’s inventory management? At Big B Business Solutions, we specialize in strategies tailored to supermarket owners and managers. Let’s work together to make your supermarket reordering process efficient and hassle-free.
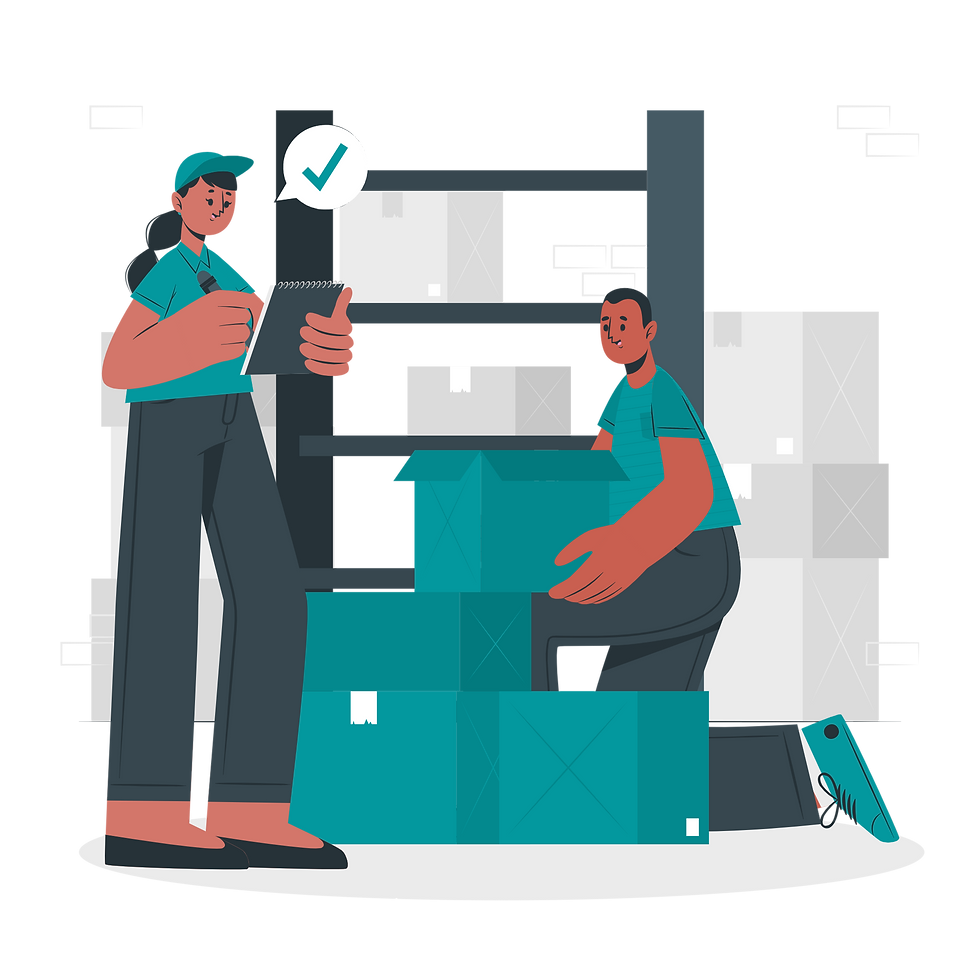
Comments